Industry 4.0 is the use of smart technologies to provide a step-change in productivity, efficiency, experience, and flexibility across the value chain of design, manufacturing, supply chain, and service. One area of loss of productivity and efficiency is the handover between two functions of design and manufacturing. Implementing design for manufacturing (DFM) by leveraging smart technologies can improve productivity and efficiency. This PoV discusses the need for DFM and highlights examples of a successful technology solution.
Read Full Publication : Download PDF
DFM minimizes defects and rework
Design for manufacturing (DFM) is a methodology that involves designing with an intent to reduce the cost of production and time-to-market, without compromising on the quality of the product. DFM minimizes defects and rework and, in the process, saves costs and shortens time to market.
Many a times, design engineers are not familiar with all the manufacturing process requirements and downstream-related parameters. Decisions made by engineers during the design stage have cascading implications on product cost, quality, and time to market. As a result, engineering changes happen too late in the cycle when issues are detected during manufacturing or assembly—and it’s costly to modify the designs.
Research indicates that around 70% of the product cost is committed during the design stage. An error detected and rectified during the design stage costs almost 100 times less than when rectified at the manufacturing stage. Sometimes, if the error gets passed into production, it can also have a direct impact in the form of costly product recalls and loss of confidence amongst customers and shareholders.
On a global average, 30% – 35% of engineering effort is spent on rework due to late design changes occurring because of downstream manufacturability and assembly issues. This rework can be avoided when DFM is followed as an integral part of the product development process.
Organization-wide DFM needs technology solutions; current DFM practices are not scalable
To implement DFM, organizations need to understand the decisions that should be made by designers when the product is getting created. There are multiple design options that should be carefully evaluated not only with respect to form, fit, and function but also by looking at manufacturing feasibility and cost of each choice. There are three key areas of design that design engineers should be cautious about while evaluating options and making choices: material choices, the geometry of features, and tolerances.
The designer needs to get feedback on cost and manufacturability during the design stage on the three points mentioned previously. The feedback may involve design reviews by senior design engineers who are familiar with the manufacturing processes, or inputs from manufacturing engineers during the design stage. Many organizations incorporate DFM practices in a checklist, which is manually verified by designers before submitting the final design.
Although organizations are managing with design reviews by experienced engineers and checklists, this method has its limitations because of which organizations are not able to leverage at scale. Some of the limitations or hurdles are:
- DFM principles are far too many to remember. It is impractical for a single person to review a design manually considering all the recommended guidelines. DFM principles mentioned in handbooks may not get referred to, and manual use of checklists can lead to errors.
- The automated mechanism for verification of knowledge transfer is missing. It takes time and effort for manufacturing engineers to transfer manufacturing-related inputs to the design team. There's no automatic verification mechanism to ensure that the inputs were incorporated in the design. This implies that the designs may have to be manually verified to validate their appropriateness.
Exhibit 1: How HCL’s DFMPro Helped Manufacturers in DFM
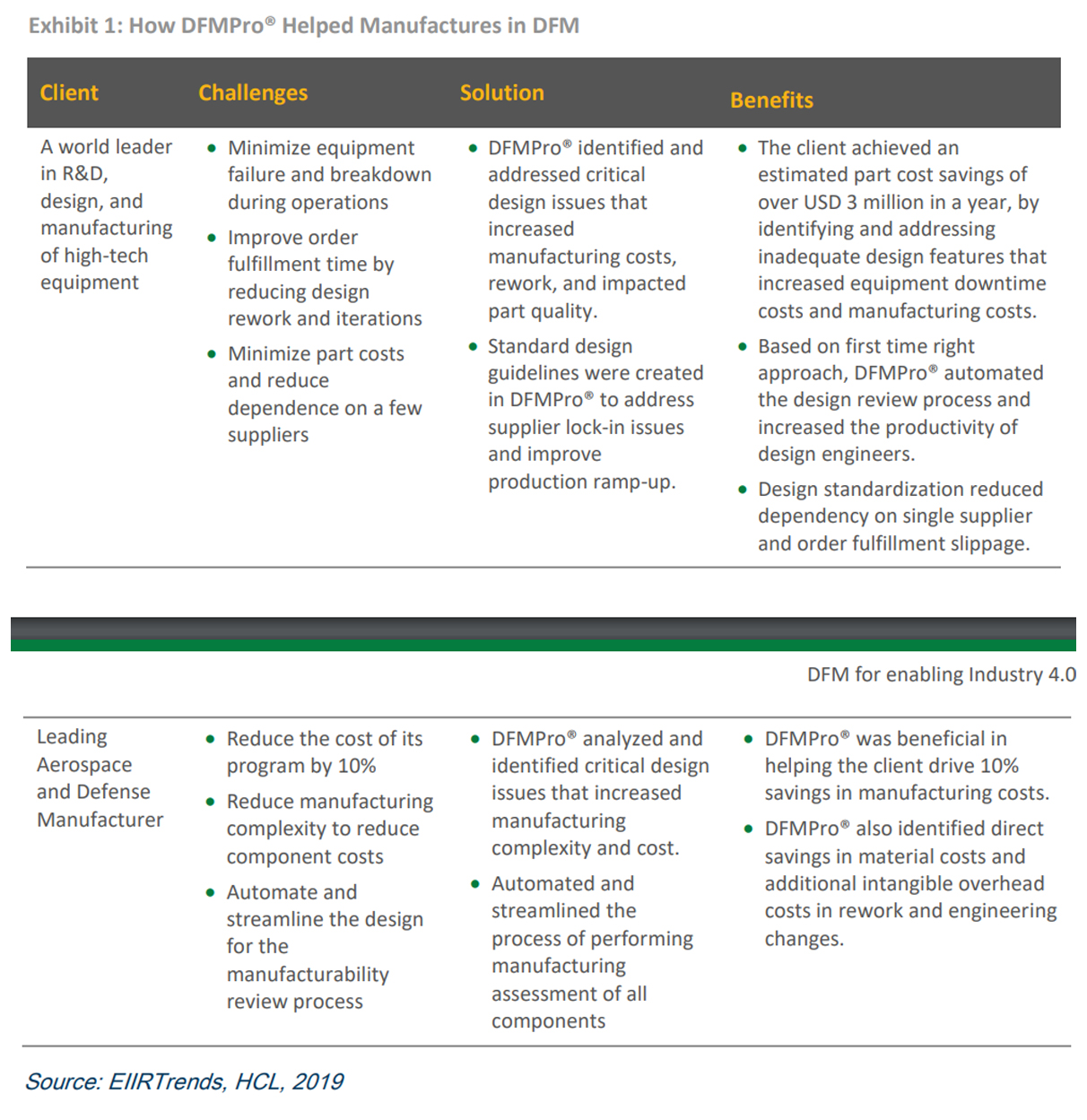